生産管理と品質管理の違いとは?AIを活用した最先端の事例もご紹介
生産管理とはモノづくりの現場で行われる受注から納品までを含む業務のことです。一言で生産管理といっても、生産計画、受注管理、発注管理、在庫管理、製造管理、外注管理、進捗管理、品質管理までの工程が含まれます。 生産管理は三つの要素である「品質」「原価」「納期」が重要です。なぜなら、高い品質の商品を、できるだけ原価を安くし、短期間で作ることが企業の利益に深く結びついているからです。 この記事では生産管理と、その一工程である品質管理の関係性を整理しながら、AIを活用した事例についても紹介します。
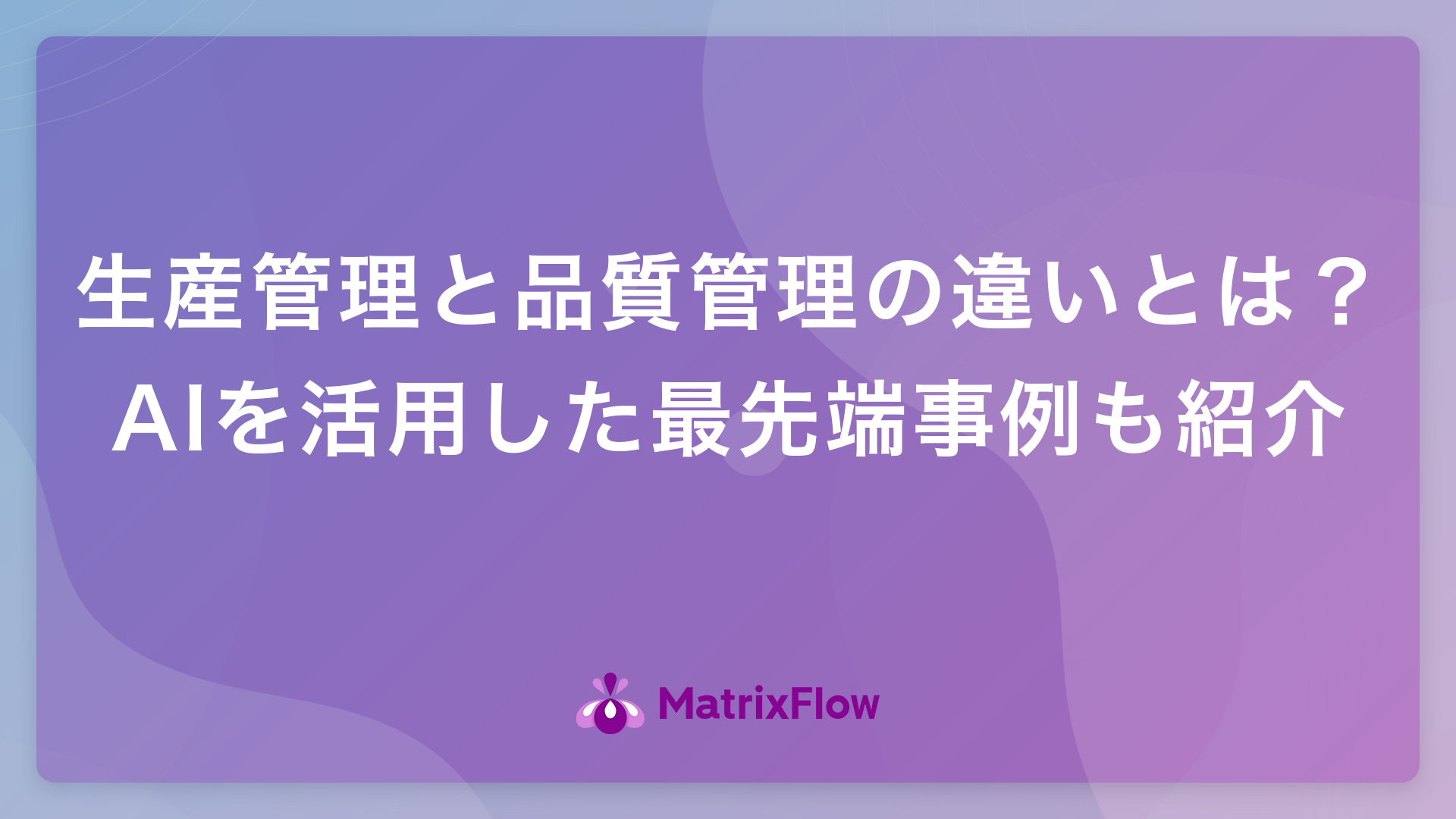
-
生産管理とは
生産管理は先に述べたように「品質」「原価」「納期」を管理し、適切な数量を生産することを目的としています。品質管理は生産管理の一部であり、「製品の品質を維持すること」が目的です。これは、いかに顧客のニーズに応えられる質をキープできるかがポイントです。
-
異なる2つの分け方で理解する品質管理
品質管理は、2つの分け方によって理解することができます。
まず工程管理、品質検査、品質改善の視点による「品質」管理方法について紹介します。工程管理、品質検査、品質改善による品質管理とは
品質管理では、工程管理、品質検査、品質改善の3種類の品質を意識して業務を進めます。以下、詳しく紹介します。・工程管理
工程管理は、まず作業手順の標準化を行うことからスタートします。また、確かな品質をキープするために製作に携わる人員の教育(作業訓練)を行います。
工程管理には、それとともに製品を作成する設備の維持管理も含まれます。また、包括してこれらの工程が正常に保たれるよう管理します。・品質検査
品質検査では、製品の品質が正しく保たれているかを検査します。製品が問題なく作り込まれているか、工程を監視し、また管理状態も適切かも合わせて監視します。・品質改善
発生した不適合の商品が再発しないよう改善を行います。それが品質改善です。そうした施策を行うことによって、不適合の商品を減らすことが目的です。
これら不適合の原因を突き止めることで、不適合の商品を未然に防ぐことにも繋がります。使用品質・設計品質・製造品質による品質管理とは
次に、使用品質・設計品質・製造品質という視点によって理解する品質管理について紹介します。・使用品質(要求品質)
「使用品質(要求品質)」とは、顧客からの要求を満たす品質のことです。・設計品質
「設計品質」とは、目標とする品質のことをさします。顧客から求められる「使用品質(要求品質)」をもとに、この設計品質を決めます。・製造品質
設計品質をもとに、実際に製造された製品の品質を「製造品質」といいます。これら各それぞれの工程に配慮した品質管理を行うことで、商品の出来栄えを一定に保つことができます。
-
生産管理・品質管理の課題とは
生産管理、その一工程である品質管理には、どのような課題があるのでしょうか。今後の高齢化社会における人材不足などの背景から、生産管理の抱える問題、課題を紹介します。
■少子高齢化による人材不足
製造業をはじめとした業界では、少子高齢化による人材不足が深刻です。そのため、後進の技術者を育てることが難しくなっています。
人材不足の加速にともない、手動での作業から脱却し、AI・ロボット化などによる技術を活用した自動化を推進する必要があります。■適正な納期管理を行うことが難しい
製造業の場合、特に納期管理を適正に行う必要があります。納期遅延はどのようなことによって起こりえるのでしょうか。
発注側の発注漏れ、誤発注(多すぎる・少なすぎる)、発注側からの手配漏れなどが考えられます。受注側にもミスが起こりうる場合があります。
このようなミスを発生させないよう、今なにがどんな状態(ステータス)にあるのかを可視化する必要があります。■正確な需要予測を行うことが難しい
需要予測とは、文字通りその商品がいつ、どのくらい必要とされているかを予測することです。その正確な需要予測があってこそ、適切な在庫管理を行うことができます。適切な在庫を管理することは、その商品を生産することである生産管理にも関係します。
過剰在庫を出さないよう、正確な需要予測を行う必要があります。■適切なコスト計算を行うことが難しい
中小企業は、大がかりなシステムを使用せずに生産管理を行っている場合があります。原価が変更された場合、その原価を正確に把握し、商品に反映する必要がありますが、そのコスト計算が適切に行われていない場合があります。
適切な価格設定をすることによって、利益の向上が見込めます。■工程・部門間の標準化が難しい
近年、1つの製品を大量生産するのではなく、顧客のニーズに合わせて多品種少量を生産する傾向が強まっています。そのため生産工程において、各部門間での標準化を行うことが課題となっています。
扱う商品が多ければ多いほど、部門間での調整量が増え、業務量が増えます。足並みをそろえてスムーズに連携すること、また標準化を行うことは難しいと言えるでしょう。 -
生産管理における品質管理の具体的方法とは
生産管理が抱える6つの問題について紹介しました。これらの「難しさ」を解決するには、どのような方法をとればいいのでしょうか。その解決方法について紹介します。
品質改善のために用いられる「新QC7つ道具」があります。問題の可視化について製造現場で日々用いられている方法です。
まず製造現場では、製品の工程・品質に関連する様々なデータを収集することができます。ただデータを集めただけではなくデータを項目別に整理するなど、相関関係などを分析することで、改善に結びつけることができます。
■親和図法
「親和図法」とは、ある課題に対する事実・意見・発想を言語データに変換する方法です。その言語データ同士を「整理」「分類」「体系化」し、「親和性」を見つけて「構造」を整理します。■連関図法
品質や現場に関わる課題を定性分析する際に役立つのが、この「連関図法」です。
「原因と結果」「目的と手段」などの相関について、それぞれの因果関係を論理的に繋いでいき、問題を解決に導く手法です。複雑に絡み合った問題の因果関係を明らかにできることが特徴です。■系統図法
目的と手段を系統づけて対策を整理する方法で、「方策展開型」、「構成要素展開型」の2種類があります。特に課題を発見しやすいという点で「方策展開型」がよく使用されています。まず左端に「目的」を設定。その右側に目的を達成するための「手段」を記載し、展開して図に表します。問題解決の具体策を見つける際に便利な方法です。■マトリックス図法
マトリックス図法とは、2つの「行」と「列」を並べ、その対応関係を記す方法です。役割分担などを決めるために使用されることの多い手法です。系統図法によって見出した施策の重みづけなどにも利用されます。■アローダイアグラム
アローダイアグラムとは、作業内容と日程の流れを表した図のことをさします。各作業の関係と日程のつながりを明確にすることで、最適な日程計画を作成することができます。プロジェクトの進行管理などにも利用されています。■PDPC法
PDPC法は、不測の事態への対応策を作成する際に利用されている方法です。「Process Decision Program Chart」の略で、「過程決定計画図」とも言われています。目標達成までの不測の事態に対応した代替案を明確にする方法で、さまざまな結果を事前に予測し、不測の事態への対応策を作成することが可能です。■マトリックスデータ解析法
マトリックス形式で集めたデータを可視化して解釈します。新QC七つ道具の中では、数値データを扱う定量的な手法でもあります。2つ以上のデータを解析することで、傾向を把握します。
複数のマトリックスを整理することで、問題の整理を行い解決策を探します。■トレーサビリティ
製品の生産・流通の履歴を追跡できることをさします。製品の品質向上に貢献するだけでなく、経路などが判明するため安全性もアップします。製造分野だけでなく幅広い分野で導入されています。■不良分析
不良分析とは、製品の不良原因の再発防止を行う技法です。不良内容の分布状況を見て推測する手法です。不良品のデータが大きく外れている場合は、なにか突発的なトラブルが起こったのだと推測できます。
そうした分析から再発防止に努めます。 -
システム化における生産管理・品質管理のメリットとは
生産管理・品質管理の課題と、その具体的な解決手法である「新QC7つ道具」のデータ分析方法について紹介しました。
次に、システム化における生産管理・品質管理のメリットについて紹介します。■業務が属人化することからの脱却
システム化をすることで、工程の標準化・均一な製品の品質管理を効率的に行うことができます。担当者の経験・勘に頼ってきた作業は、業務の属人化、退職によって技術が失われるリスクがあります。しかし、システム化をすることによって、そのようなリスクから脱することができます。■管理コストを削減できる
生産管理をシステム化することで、正確にコスト管理が可能になります。そのため販売価格に対して一定の利益率を確保ができるようになります。
データによる可視化ができるため、原材料の仕入れ価格・調達先の見直しが容易になります。■製品・サービスの追跡(トレーサビリティ)
トレーサビリティにより、製品・サービスが追跡可能になると、原料の仕入れ先、その原料が仕入れられたタイミング、生産場所、価格、製造崎の工場、そのラインの責任者などその製品・サービスが作られた工程のすべてがデジタルに記録されることになります。
その記録データは必要に応じてチェックが可能なため、品質に問題が起きたときやトラブルが発生した場合、遡って調べることができます。
また製品にICタグをつけることで、適切な在庫管理ができるようになり、棚卸しなどの作業も簡略化できます。■データ収集・分析の自動化
システム化することにより、工程すべてがデータ化できます。それにより大量の作業データを得て分析をすることができます。
そうした分析は、不良品の検出などに役立てることができます。 -
AI活かせる品質管理の領域4つ
システム化したことで得られたデータを、AIを使用することで品質管理に活かすことができます。では、どのように品質管理に貢献できるのでしょうか。その領域を4つ紹介します。
■異常検知
AIが得意とするものに、異常を予測できることが挙げられます。その精度の高さによってもAIは注目を浴びています。
異常検知とは、正常な状態とは異なる状態・状況を検知、検出、予知することです。過去の異常を検出した際のデータをAIに学習させることによって、異常予測、故障予測、故障予知、予兆検出などができるようになります。AIの進歩も進んでいますが、現在は先に述べたように学習データを必要とする「教師あり学習」が主流となっています。そのため、「人の目でわかる異常の検知を機械に任せる」といった使い方をされています。
具体的には、画像をもとに見た目でわかる異常や欠落、破損などを検出することを目的にしたAI活用が進んでいます。ほかには製造機械の異音を検知するといった音声AIを活用するケースも見られます。
■外観検査
異常検知のひとつで、文字通り外観にキズがないか画像データを用いてAIに検出させる検査です。
難しさの1つに、AIにどのようにキズを判定させるか、という点があります。
なぜなら同じ製品の写真であったとしても、撮影の角度、明るさ、画素数などの解像度が異なる場合、AIにとってはまったく別物であると認識されるおそれがあるからです。
そのため、キズの有無だけにフォーカスできるような撮影環境を整えることが重要となります。AIが正しくキズを判定するためには、その許容範囲を定めるなどして反映・評価ロジックを構築する必要があります。そうしたルール作りがきちんとできていないと、たとえAIを導入したとして「不良品」として誤判定された製品の山ができてしまうでしょう。
また外観検査にAIの判定のみを持ち込むのではなく、その後の業務オペレーションを考えるなど、総合的な業務の再設計も必要になります。■安全管理
作業員の安全を確保する安全管理にもAIが活かされています。工場には大型の機械なども多く、判断を誤ると作業員の大きな怪我、また事故にも繋がる恐れがあります。ここで言う安全管理は、製品を作るための機械・設備の管理という意味ではなく、人命を守るための安全管理のことです。
安全管理にAIを活用することで、担当者の勘に頼らず、新人であっても危険を回避することが可能となります。■工程最適化
製造業、流通業などでは、複数の工程があります。これをいかに効率的に運用するかについて、AIを活かすことができます。
具体的には、トラックの配送ルートの策定などがあげられます。近年では、強化学習を用いて組合せ最適化問題を解決するケースもあります。 -
生産管理・品質管理で使えるAIサービス「MatrixFlow」
生産管理・品質管理の概要と、AIの活用方法などについて紹介しました。生産管理の効率化にはシステムの見直しとDX化が欠かせませんが、そのための投資の金額に躊躇する企業も多いことでしょう。
ビジネスのためのAI活用プラットフォーム「MatrixFlow」(マトリックスフロー)は、プログラミング不要で、ドラッグ&ドロップをするだけで誰でも簡単に機械学習を使いこなすことができます。AIモデルを簡単に作成できることから、先に述べた異常検知・外観検査・工程最適化・安全管理の領域で効率化を図ることが可能です。また、生産管理システムへの実装もできることが特徴です。
編集部Pickup記事
-
ノーコードでAIを開発する方法とは?開発事例・無料の開発プラットフォームを紹介
ここ数年、国内外の開発者の間で「ノーコード(NoCode)」という言葉がよく聞かれます。 ノーコードとは、文字通りコードいらずでWebサイトやWebサービスを開発する手法のことです。 このノーコードの開発手法を使って、AI(人工知能)を開発しようとする動きが出てきています。 本記事では、ノーコードでAIを開発して自社課題を解決したい方に向けて、ノーコードでどんなことができるのかを解説していきます。 ノーコードを使ってAIを開発した事例も紹介しているので、ぜひ参考にしてみてください。
-
機械学習のビジネスにおける活用事例を徹底解説
様々な分野・企業で、AIや機械学習の活用が進んでいます。 iPhoneのSiriやGoogleのアレクサなど、日常生活にも溶け込んでいるほどです。 AIにデータを機械学習させれば、膨大な時間がかかる作業も分析も一瞬で終えることができます。 AIは学習させるデータでどんな使い方もできるため、その可能性は無限大です。 本記事では、AIや機械学習をビジネスに活用する方法や、導入事例をご紹介します。
-
AIツール・開発プラットフォームおすすめ13選!無料AIツールも?
AI(人工知能)を使ったツールやアプリは、ここ数年で急激に増えました。身近なところだと、有名画家風のイラストが作成できるアプリや音声読み上げソフトなど、一度は耳にしたことがある方もいるのではないでしょうか。 企業においても課題解決ができるAIツールや、AIを開発できるプラットフォームへ注目が集まっています。ですが、AIツールと一口にいっても、開発できるAIの種類や解決できる課題も様々です。 本記事では、AIを開発できるプラットフォームや、無料で使える便利なAIツールをご紹介します。AIツールを使ってどんなことができるのか、ツールによる違いを知りたい方は必見です。
-
AIによる需要予測の仕組みとは?導入事例・費用・アルゴリズムを解説
過去の販売データを元に商品の発注数や売れ行きを予測するのは、小売業界では当たり前に行われています。 ですが、経験や勘に頼った予測は個人の力量に依存するため、予測に再現性がありません。予測の精度も人によってバラバラなため、常に高い精度で予測することは難しいです。 こうした課題を解決する方法の1つとして、AIを使った需要予測が注目されています。AIを使うことで、スキルに依存しない高精度で需要予測が期待されているのです。 本記事では、AIを使った需要予測の仕組みや導入事例について解説していきます。需要予測をして在庫管理の最適化や売上増加を狙っている方は、ぜひ参考にしてみてください。
-
製造業におけるAI活用事例23選!各社の導入方法・例をご紹介
ここ数年でAi技術は格段に進化を遂げています。様々な領域でAIの活用が進んでいますが、製造業ではどのくらいAIの導入が進んでいるのでしょうか。製造現場での実用化にはいまだ課題も残っています。AIを活用できる人材がいない、AIの導入方法がわからず、活用が進んでいない企業も多いのではないでしょうか。 この記事では、実際にその仕組みや導入のメリット、成功・失敗事例を紹介していきます。製造業でAIを導入するうえでの注意点についても解説していますので、ぜひ参考にしてください。
-
ディープラーニング(深層学習)とは?AI・機械学習との違いを簡単に解説
ディープラーニング、AI、機械学習。誰しも、テレビや本で一度は耳にしたことがあると思います。 ですがこれらが何を指しているのか、なぜ注目を集めているのか知っている方は少ないのではないでしょうか。 本記事ではAIを学んだことがない方向けに、ディープラーニングとは何なのかを簡単に解説します。 ディープラーニングと機械学習の違いがわからない方や、ディープラーニングの活用事例を知りたい方も必見です。
関連した事例
-
予測分析ツールおすすめ7選比較!AIで予測できること・無料ツールはある?
将来の売上や株価を予測することができれば、ビジネスや投資において非常に有利に動けます。しかし、人の勘や経験に頼った予測には限界があり、正確な予測をすることは困難です。 そこで、あらゆる業界で「予測分析ツール」が注目されています。予測分析ツールを使えば、膨大なデータを分析し、過去の傾向をもとに未来を予測できます。さらに、機械学習や人工知能を使った予測分析ツールを活用すれば、誤差を減らしてより高い精度で予測を行うことができます。 本記事では、予測分析ツールでどんなことが予測できるのか、おすすめの予測分析ツールをご紹介します。AIやツールを使った予測に興味がある方は、ぜひ参考にしてみてください。
-
AI開発外注の費用相場・期間は?おすすめ開発会社を解説
AIを開発したいと思った時にまずぶつかる壁は、「自社内で開発するか外注するか」です。 社内に開発人材がいる場合もいない場合も、AI開発の外注は選択肢の1つとして考えられます。 AI開発の外注にはメリット・デメリットがあるため、AI開発において重視する内容によって外注が最適かどうか変わってきます。 本記事では、AI開発を外注しようか検討している方に向けて、AI開発の外注にかかるコストやメリット・デメリットを解説します。さらに、AI開発に強いおすすめの外注先もご紹介するので、開発会社選びの参考にしてみてください。
-
ノーコードでAIを開発する方法とは?開発事例・無料の開発プラットフォームを紹介
ここ数年、国内外の開発者の間で「ノーコード(NoCode)」という言葉がよく聞かれます。 ノーコードとは、文字通りコードいらずでWebサイトやWebサービスを開発する手法のことです。 このノーコードの開発手法を使って、AI(人工知能)を開発しようとする動きが出てきています。 本記事では、ノーコードでAIを開発して自社課題を解決したい方に向けて、ノーコードでどんなことができるのかを解説していきます。 ノーコードを使ってAIを開発した事例も紹介しているので、ぜひ参考にしてみてください。
-
ディープラーニング(深層学習)とは?AI・機械学習との違いを簡単に解説
ディープラーニング、AI、機械学習。誰しも、テレビや本で一度は耳にしたことがあると思います。 ですがこれらが何を指しているのか、なぜ注目を集めているのか知っている方は少ないのではないでしょうか。 本記事ではAIを学んだことがない方向けに、ディープラーニングとは何なのかを簡単に解説します。 ディープラーニングと機械学習の違いがわからない方や、ディープラーニングの活用事例を知りたい方も必見です。
-
プログラミングでAIを開発する方法!必須のプログラミング言語・入門知識を解説
近年急速に進化しているAI(人工知能)。 AIを活用すれば、今まで大量の人と時間を投下していた業務も効率よく精度高く遂行できます。 人と同じような動きができるためすごい存在に思えるAIですが、プログラミングを学べば初心者でも開発が可能です。 本記事では、プログラミングをしてAIを開発する方法やAI開発におすすめのプログラミング言語をご紹介します。
-
機械学習(ML)とは? メリット・種類・業界や課題別の活用例・実施方法を解説
機械学習(Machine Learning)とは、コンピューター(Machine)が与えられた大量のデータを処理・分析することでルールやパターンを発見する技術・手法のことです。学習の結果明らかになったルール・パターンを現状に当てはめることで、精度の高い将来予測が可能となります。 高度なコンピューターを使用することで、人間の脳では処理しきれない複雑な要素を加味した分析・学習が可能となりました。その結果、近年ではさまざまな領域において人間による作業の精度向上・効率化に役立てられています。自動運転や医療、人間の購買行動の分析など、さまざまなビジネス領域で機械学習が実用化されており、今後のマーケットで生き残っていくためには必須の技術になりつつあるといえるでしょう。 本記事では、機械学習(ML)の概要やメリット、種類に加え、業種別・課題別の活用例を紹介します。実際に取り入れる際の作業フローも紹介しているので、機械学習の活用に興味がある方はぜひ参考にしてみてください。
-
データドリブン経営とは?成功事例からわかる必要性・メリット解説
ビジネスでデータを活用するのは、今やどの企業も当たり前に行なっています。 ですが、データを効果的に活用できている企業はあまり多くありません。 データを部分的にしか活用できていない、人によってデータ活用のレベルが異なる企業が多いのではないでしょうか。反対に、データを活用しようと意気込んで収集した結果、膨大なデータを持て余している場合も見受けられます。 このように、データを有効活用できていないと感じる方々に知っていただきたいのが、「データドリブン経営」という考え方です。本記事では、データドリブン経営とは何かを簡単に解説し、データドリブンで数字改善した成功事例をご紹介します。データを活用して売上を伸ばしたい、コスト改善したいと考えている方は、ぜひ参考にしてみてください。
-
AIやExcelを活用したコールセンターの入電数予測の方法
コールセンターにおけるコール予測(呼量予測、forecaster)とは、お客様からの問い合わせなどセンターで受信する電話の量を予測することをいいます。 コールセンターの運用コストを増加させる要因のうち大きなものが、コミュニケーターの人件費です。コミュニケーターは顧客からの入電に応じてオペレーションの対応をするため、実際の入電数よりも多くのコミュニケーターを配置すると、対応がなく待ち状態のコミュニケーターが増えて、不要な人件費の増加に繋がります。また、逆に配置人数が少ないと呼び出し中でつながらないなどのクレームの要因になりかねません。適正な人員をコンタクトセンターに配置することで、十分な顧客満足度が提供できる状態でオペレーションを行っていることが理想です。今回は、Excelを活用したコール予測、AI(人工知能)による機械学習を用いた時系列分析で、コール予測を実現する方法をご紹介します。
-
予測分析とは?活用事例とその手法・ツールをご紹介
予測分析とは、過去の行動パターンを特定し、将来の結果を予測するために、大量のデータに数理モデルを適用する手法です。 機械学習、データマイニング、統計アルゴリズムなどの複数の組み合わせがもたらす「予測的手法」により、予測分析ツールは、単純な相関付け以上の機能を実装できます。ビジネス分野では、予測分析が以下に示すようなさまざまな用途に利活用されています。 ・需要と供給のより正確な予測コンピューターネットワークに悪影響を及ぼす脅威と潜在的問題の特定 ・保険サービスや金融サービスにおけるセキュリティリスクの低減 ・クレジットカード詐欺のリアルタイム検出 予測分析機能を組み込んだソフトウェアが増えつつあり、これはあらゆる規模の組織体でユーザーにとって身近なものになっています。予測分析はデータサイエンスや高度な分析に関する訓練を受けていないエンドユーザーにも実務上の価値をもたらします。これは、まさにすべてのユーザーが恩恵を受ける機会を提供することに値します。この概念を「データの民主化」と呼びます。誰もがデータを利用してより良い意思決定を下せるように、組織全体でデータを誰もが利用できるようにするという概念です。 本記事では、予測分析がなぜ重要なのか、予測分析の実活用例、予測分析の手法、機械学習やデータマイニングなどの他のテクノロジーとの関係、モデルの役割、予測分析を始めるにあたってのヒントについてご紹介します。